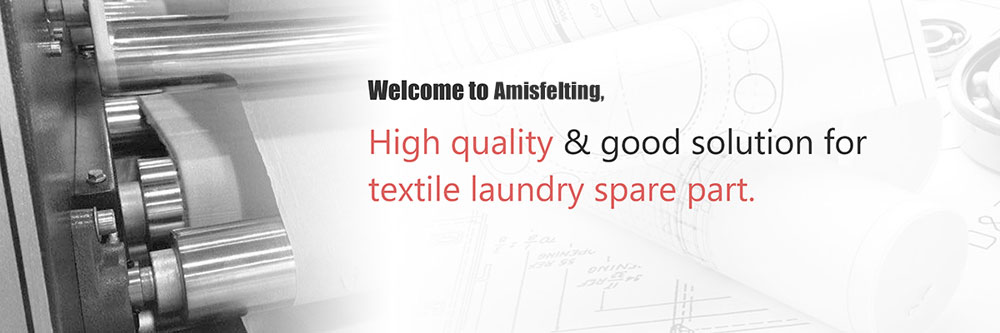
- 作者:
- 来源:
- 日期: 2016-02-26
- 浏览次数: 2526次
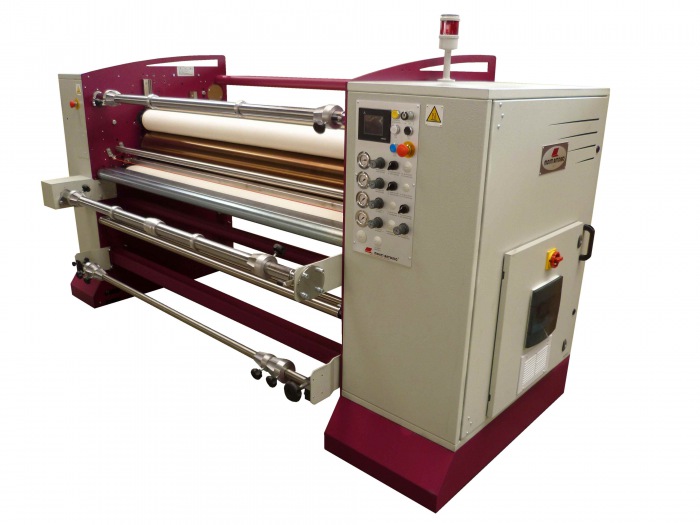
Thermal transfer printing is the use of the principle of sublimation of disperse dyes or inks. Paper is used as a carrier to transfer the pattern printed on the paper to the fabric by sublimation of temperature. The most important part of heat transfer printing is that the dye should be sublimed under certain temperature and pressure conditions. Because the Tencel fabric is printed with reactive dyes, it does not need high temperature and high pressure, and does not have sublimation conditions. Therefore, the silk fabric printing mainly uses watermarks and digital , can not use the thermal transfer printing process.
1. Classification and process principle of thermal transfer printing. Thermal transfer printing is usually divided into hot melt transfer printing and thermal sublimation transfer printing. Hot-melt transfer printing is commonly used in cotton products, with the disadvantage of poor hand permeability. Sublimation type transfer printing is often used for transfer printing of polyester. The disadvantage is that the plate making cost is high. The most commonly used method for thermal transfer printing is the sublimation method. The principle is to transfer the disperse dye to synthetic fibers such as polyester and fix it under high temperature conditions by using the sublimation characteristics of the disperse dye. The specific process is to pass the pattern through the plate roller or flat net after printing, or it can be a rotary screen printing machine to print on the paper with disperse dye or ink. Then, the transfer printing paper with the pattern printed on the transfer printing machine and the fabric will be combined under the suitable temperature and pressure conditions to physically and chemically transfer the pattern on the paper to the surface of the fabric, and diffuse and penetrate into the fiber. The inner layer is fixed. This is the current process of thermal transfer printing on polyester fabrics. Sublimation-type transfer printing can be divided into different printing methods: offset printing, gravure printing, silk screen printing, and data printing.
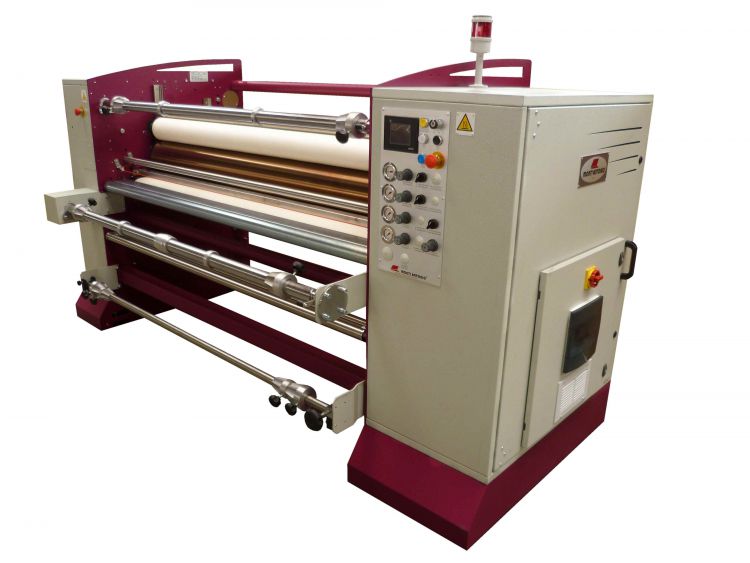
2. Advantages and disadvantages of thermal transfer printing.
1). The advantage of thermal transfer printing is that compared with the traditional process, the heat transfer printing has a small footprint and a short process flow; because the disperse dye is used for sublimation and fixing, the color is completely fixed; the post-treatment of fixing, washing and the like is reduced. The process, thus eliminating the problem of sewage, is an environmentally friendly printing and dyeing method. Since the amount of liquid absorbed by the transfer printing base paper is much less than that of the direct printing on the fabric, the cost is relatively reduced. The complex color matching and pattern-making defects can be found in the printing of paper, and the rickets can be cut off before being transferred to the fabric, thus ensuring the highest authenticity rate of the finished fabric after transfer. The transfer printing is very small due to the broadness of the base paper. The pattern of the transfer printing cloth is clearer, the layers are more distinct, and the color is more uniform. The three-dimensional effect is strong, especially in the halftone effect.
2). The disadvantages of heat transfer printing are: suitable for small batch, multi-variety, short delivery products. Fiber applications have limitations. High temperature and high pressure are required in the transfer process, so it is mainly used for chemical fiber fabrics, mainly polyester fiber. It is difficult to achieve very satisfactory scale production on natural fibers such as cotton and silk, and regenerated fiber fabrics such as Tencel, human silk, human cotton, modal, and copper ammonia. Therefore, the Tencel fabric does not use thermal transfer printing. In addition, the heat transfer printing transfer paper is required to be high and used in a large amount.
3. Conditions for thermal transfer printing.
1). Transfer temperature. The temperature depends on the optimum temperature of the sublimation dyeing of the dye, the heat resistance of the fiber, and the heat transfer time. For disperse dyes used in thermal transfer printing, the sublimation temperature should be lower than the melting point of fiber macromolecules and the strength of the fabric should not be damaged. The suitable processing temperature for polyester is 180-210 °C. In this temperature range, the molecular weight of the dye sublimation is between 230 and 270 °C. Because the temperature is too high, it is not suitable for Tencel, so the Tencel fabric cannot be printed with heat transfer.
2). Transfer pressure. Flat plate printing machine: 10kPa as the standard transfer pressure, if the pressure is insufficient, the transfer paper and the printed fabric are not tightly matched, the printed pattern is uneven, and the color is not clear; otherwise, if the pressure is too large, The feel and style of the printed fabric will also change. Pressure is also not suitable for Tencel, which is one of the reasons why Tencel fabric does not use thermal transfer printing. Roll transfer printing machine: In order to make the transfer paper and the printed fabric have a close coincidence, the felt must be tightly coated on the surface of the heat roller, and the suitable pressure is generally controlled at 12 kPa. Vacuum negative pressure heat transfer machine: Under the condition of negative pressure (13.3 kPa), good coloring and penetrating effect can be obtained, and the texture of the printed fabric is very good.
3). Transfer time. In actual processing, the transfer time is 15~45s. The transfer temperature, the type of fiber, the texture and the variety of the woven fabric and the knitted fabric all affect the transfer time.
4. Color fastness. The color fastness of the heat transfer printing fabric mainly depends on the following three factors: the processed fabric; the transfer paper used, and the dye printed on the transfer paper; and the process conditions of the transfer printing.