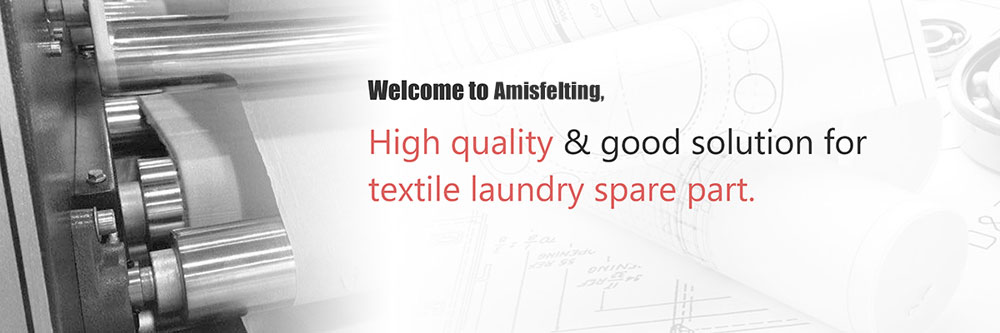
- 作者: Emily
- 来源:
- 日期: 2019-06-18
- 浏览次数: 1016次
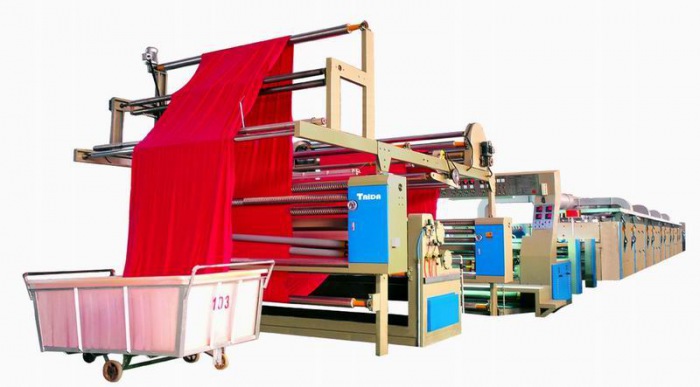
Finishing is a technical treatment method that gives the fabric a color effect, a morphological effect (smooth, suede, stiff, etc.) and a real effect (watertight, non-felting, non-scalding, non-sticking, flame-resistant, etc.). The process of improving the appearance and feel of the fabric by chemical or physical main methods, improving the performance of the fabric or imparting special functions, is the processing process of the textile "the icing on the cake".
The finishing method can be divided into two categories: physical/mechanical finishing and chemical finishing. According to the purpose of finishing and the different effects, it can be divided into basic finishing, appearance finishing and functional finishing.
Purpose of #finishing
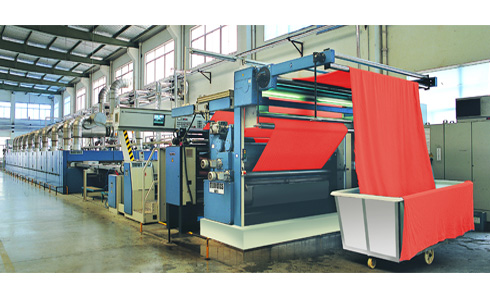
1. The textile width is uniform and uniform, and the size and shape are stable. Such as fixed (pull), mechanical or chemical anti-shrinkage, anti-wrinkle and heat setting.
2. Enhance the appearance of textiles: including increasing the gloss and whiteness of textiles, and enhancing or reducing the surface fluff of textiles. Such as whitening, calendering, electro-optic, Asian, sanding, shearing and shrinking.
3. Improve the feel of textiles: Chemical or mechanical methods are used to give textiles a comprehensive touch feel such as softness, smoothness, fullness, stiffness, lightness or thickness. Such as soft, stiff, weight gain and so on.
4. Improve the durability of textiles: mainly use chemical methods to prevent damage or erosion of fibers caused by sunlight, atmosphere or microorganisms, and prolong the service life of textiles. Such as anti-mite, anti-mildew finishing.
5. Give textiles special properties: including some protective properties or other special functions. Such as flame retardant, antibacterial, water repellent, oil repellent, anti-UV and antistatic.
The development of fabric finishing technology is towards product functionalization, differentiation, high-grade, diversified and deepening of processing technology, and emphasizes improving the performance of products and increasing the added value of products. In recent years, we have continuously introduced new technologies (such as low temperature plasma treatment, bioengineering, ultrasonic technology, electron beam radiation treatment, inkjet printing technology, microcapsule technology, nanotechnology, etc.) from other technical fields to improve processing. Depth, get a good finishing product. With the concern of human beings for environmental pollution and destruction, more and more attention is paid to health, and a “low-carbon” economy is advocated. The finishing technology requires environmentally-friendly “green” processing to produce “clean” and “low-carbon” textile products.
The basic finishing methods of fabrics include: stable size, improved finishing method, finishing method for improving hand feeling optimization performance, multi-functional, high value-added finishing methods for fabrics, finishing methods for advanced fabrics, and special requirements. Finishing method.
Various finishing processes are as follows:
1 pre-shrink
Pre-shrinking is a process that physically reduces the shrinkage of the fabric after immersion in water to reduce shrinkage. The mechanical pre-shrinking is to first wet the fabric by spraying or spraying, and then applying mechanical warp to increase the buckling wave height, and then loosely drying.
2 tenter
Stretching is a process that utilizes the plasticity of cellulose, silk, wool and other fibers under wet conditions, and gradually widens the width of the fabric to a specified size for drying, so that the fabric shape is stabilized, also known as fixed-width finishing.
3 sizing
Sizing refers to a finishing process in which the fabric is dipped in a slurry and dried to obtain a thick and stiff feel.
4 heat setting
Heat setting is a process for making thermoplastic fibers and blended or woven fabrics relatively stable. It is mainly used for the processing of synthetic fibers such as nylon or polyester which are easily shrink-conformed after heating and their blends. The heat-set fabric improves dimensional stability and feels stiff.
5 whitening
Whitening is a process of increasing the whiteness of textiles by using the complementary color principle of light, also known as whitening. The whitening method has two kinds of blue and fluorescent whitening.
6 calendering, electro-optic and embossing
Calendering is a process in which the surface of a fabric is flattened or rolled out of parallel fine twill by utilizing the plasticity of the fiber under moist heat conditions to enhance the gloss of the fabric. The flat rolling light is composed of a hard roll and a soft roll to form a hard rolling point. After the fabric is rolled, the yarn is flattened, the surface is smooth, the gloss is enhanced, and the hand feels stiff. The soft calendering is composed of two soft rolls which form a soft rolling point. After the fabric is rolled, the yarn is slightly flat, the gloss is soft and the hand feels soft.
Electro-optic is the use of electrically heated rolls to calender the fabric.
The embossing is composed of a steel roll and a soft roll engraved with a emboss pattern, and under the hot rolling condition, the fabric can obtain a lustrous pattern.
7 velvet, sanding
The process of grinding a short and dense pile of wool on a surface of a fabric with a sanding roller (or belt) is called a sanding, also known as sanding. The sanding finishing enables the warp and weft yarns to simultaneously produce fluff, and the pile is short and dense.
8 hairs
Fleece is a process of picking up the fibers of the surface of the fabric with dense needles or thorns to form a layer of fluff, also known as brushed finishing. The fluffing is mainly used for woollen fabrics, acrylic fabrics and cotton fabrics. The fluff layer enhances the warmth of the fabric, improves the appearance and makes the hand feel soft.
9 shearing
Shearing is the process of cutting off the unwanted hair on the surface of the fabric with a shearing machine. The purpose is to make the fabric texture clear, smooth surface, or to make the fluff or pile surface of the raised and napped fabrics neat. Generally, wool, velvet, artificial fur, and carpets need to be sheared.
10 soft
The soft finishing has two methods of mechanical finishing and chemical finishing. The mechanical soft finishing is realized by bending the fabric several times, and the softening effect after finishing is not satisfactory. The chemical softening treatment is to apply a softening agent on the fabric to reduce the coefficient of friction between the fibers and the yarn, thereby obtaining a soft, smooth hand feeling, and the finishing effect is remarkable.
Source: Announced Network, Printing and Dyeing Online Communication