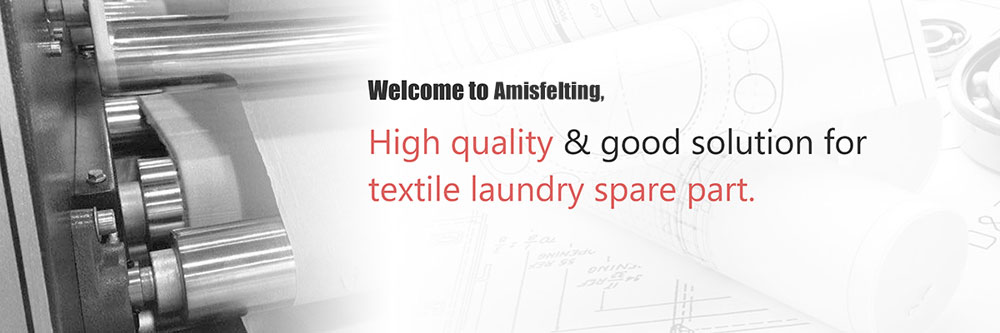
- 作者: Emily
- 来源: 傅博士
- 日期: 2019-06-08
- 浏览次数: 1700次
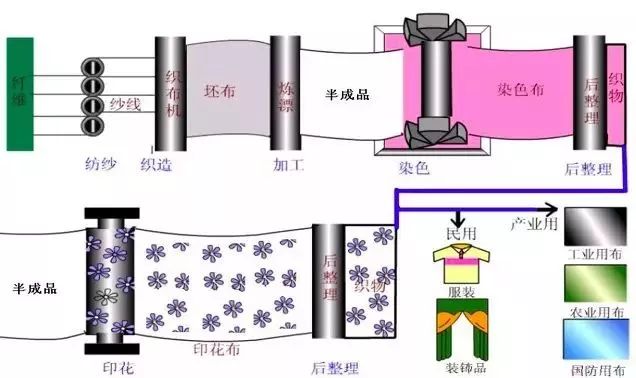
The selection of dyeing and finishing process is mainly based on the variety, specifications and finished product requirements of the fabric, which can be divided into pre-treatment, dyeing, printing and finishing.
Pretreatment
Natural fibers contain impurities. In the textile processing process, various pastes, oils and contaminated dirt are added. The presence of these impurities not only hinders the smooth progress of dyeing and finishing, but also affects the wearing performance of the fabric.
The purpose of pretreatment is to apply chemical and physical mechanical action to remove impurities on the fabric, make the fabric white and soft, have good penetrating properties, meet the requirements of taking, and provide qualified semi-finished products for dyeing, printing and finishing.
Cotton: original cloth preparation, singeing, desizing, scouring, bleaching, mercerizing.
Polyester: preparation of grey fabric, refining (liquid alkali, etc.), pre-shrinkage, predetermined type, alkali reduction (liquid alkali, etc.).
Singeing
Usually, after entering the printing and dyeing factory from the textile mill, the grey fabric should first be subjected to inspection, tumbling, batching, printing and sewing, and then singeing.
the reason:
1 Unburned cloth has too many fluffs and varies in length;
2 poor finish, easy to stain;
3 It is easy to lose hair in the subsequent dyeing and finishing process, resulting in printing and dyeing.
Singeing purpose
1 Improve the gloss of the cloth; improve the finish;
2 improve the anti-pilling performance (especially chemical fiber fabric);
3 improve the style, singeing will make the fabric become crisp and bone.
Desizing
During the weaving process, the warp yarns are subjected to large tension and friction and are prone to breakage. In order to reduce the warp and improve the weaving efficiency and the quality of the fabric, the warp yarn needs to be sizing before weaving, which is the fiber adhesion and cohesion in the yarn, and forms a strong slurry film on the yarn surface to make the yarn tight and Smooth, thereby increasing the breaking strength and wear resistance of the yarn.
Desizing purpose: After sizing, the slurry penetrates into the fiber and is partially attached to the surface of the warp yarn. While improving the yarn performance, the slurry contaminates the dyeing and finishing fluid, hinders the chemical interaction between the fiber and the dyeing material, and dyes the dye. The whole process is difficult to carry out.
First, the introduction of common slurry
Natural pulp: starch, seaweed gum, gum, etc.
Starch properties: 1 acid decomposition, 2 alkali stable, swelling, 3 oxidant can be decomposed, 4 is decomposed by starch decomposing enzymes.
Chemical slurry: cellulose derivatives such as hydroxymethyl cellulose (CMC), polyvinyl alcohol (PVA), polyacrylic acid, polyester, and the like.
PVA properties: 1 is stable to acid and alkali, and viscosity is not lowered. 2 is degraded by oxidants. 3 Wide applicability, good compatibility, no reaction.
Second, the common desizing method
1. Alkali desizing
One of the most widely used methods in domestic dyeing factories, but the desizing rate is not high, and other impurities can be removed in the same fashion as desizing.
Mechanism: treated with dilute sodium hydroxide solution, the starch slurry swells (or puffs) under the action of alkali, and no chemical reaction occurs, which causes the slurry to transform from gel to sol, reducing fiber to slurry. The bonding force is then removed by washing with water and mechanical force. For PVA and polyacrylate-based slurries, it is capable of dissolving a dilute sodium hydroxide solution.
2. (starch) enzyme desizing
Enzymes are also known as enzymes, biocatalysts.
Features: high desizing rate, no damage to fiber, only starch, can not remove impurities.
Features: a. High efficiency. b. Specificity, an enzyme can only catalyze a reaction or even a specific reaction. c. Activity is affected by temperature and pH.
For starch slurry or starch mixed pulp (starch content is dominant), amylase can be used for desizing.
3. Acid desizing
There are not many domestic applications, because it is easy to damage the fibers during use, and it is often used in combination with other methods.
A two-step process is used: alkali desizing - acid desizing.
Acid desizing can hydrolyze starch, remove mineral salts and other functions, and make up for each other.
4. Oxidation desizing
Oxidizing agent: NaBrO2 (sodium bromate) H2O2, Na2S2O8, (NH4)2S2O8, and the like.
Principle: The oxidant can oxidize and degrade various kinds of slurry, its molecular weight and viscosity are greatly reduced, water solubility is increased, the slurry is prevented from adhering to the fiber, and then the hydrolyzed product is removed by high-efficiency water washing.
Culinary
The purpose of scouring is to remove fiber impurities and improve fabric processing properties, especially wetting properties.
Natural impurities: For cotton fabrics, mainly fiber commensal or companion organisms, including oil wax, pectin, protein, ash, pigment and cottonseed hull.
Artificial impurities: oils, antistatic agents, and impurities such as oil, rust, and residual slurry added in the spinning and weaving process.
These impurities seriously affect the wettability of the fabric and hinder the processing of the dyeing and finishing of the fabric, and must be removed in a scouring system mainly composed of sodium hydroxide and a surfactant.
#dyeing #finishing #Textile